Sustainability April 05, 2024
Lululemon Develops ‘Enzymatically Recycled Polyester’ Jacket
Plus, a running shoe company shows off 3D-printed, compostable footwear, and IKEA turned its old uniforms into cushions and other home goods.
Popular activewear brand Lululemon has launched its first product made with “enzymatically recycled polyester,” an innovation it says marks another key milestone in textile-to-textile recycling and a step forward in its efforts to create a circular ecosystem.
This packable anorak from Lululemon is made from “enzymatically recycled polyester.”
The limited-edition packable anorak is part of a multi-year collaboration with Australian enviro-tech startup Samsara Eco, and it features polyester made from a combination of bioprocessing technologies, including enzyme-based recycling from Samsara Eco and captured carbon emissions from LanzaTech.
Recycled polyester has become increasingly common in the fashion world, but the majority of it is recycled polyethylene terephthalate (rPET), made from transforming plastic bottles into pellets, which are then spun into thread. Recycling old textiles into new fabric has been more elusive, though it’s something many brands have been exploring.
Samsara Eco’s technology uses enzymes to break down the complex synthetic blends that are used extensively in the performance apparel industry. LanzaTech specializes in capturing carbon emissions from industrial facilities and converting them into building blocks for polyester, according to Lululemon. The anorak, which is made with mixed plastic waste, Lululemon apparel at the end-of-life stage, and converted carbon emissions, demonstrates the company’s circular design philosophy.
“Our vision is to scale this technology to address textile waste across our entire supply chain,” said Yogendra Dandapure, vice president of raw materials innovation at Lululemon. “This capsule product is a first step along this journey, helping us test and learn as we continue to advance circularity, which signals exciting possibilities for all industries looking to shift to more circular models.”
Vivobarefoot Creates Biodegradable, 3D-Printed Footwear
Vivobarefoot collaborated with material science company Balena to make a 3D-printed, compostable shoe.
B Corp-certified Vivobarefoot recently collaborated with Balena, a material science company, to develop a 3D-printed, custom-designed shoe made to fit your natural foot shape. The shoe, made of Balena’s proprietary BioCirflex thermoplastic material, is designed to be durable and high-performance, but is also able to be broken down at the end of life through controlled biodegradation in industrial compost facilities, according to the company.
“The objective is to create a footwear ecosystem that is made-to-order and made-to-measure, produced locally and with minimal environmental impact,” according to Forbes.
Vivobarefoot also recently launched a more conventional-looking sneaker, the Gobi Sneaker Premium, noting on its website that it’s anything but a “normal sneaker.” Made from 98% natural materials, the shoe features cork insoles, organic cotton laces, chrome-free leather and pliant outsoles made from 100% biobased rubber derived from rubber tree milk in certified forests. Unlike with traditional processes, the outsoles use a plant-based curative, making them circular and recyclable by NFW, the company that manufactures them.
Old IKEA Uniforms Upcycled Into Cushions & Curtains
IKEA recycled old uniforms, turning them into raw materials that could be made into new home goods.
Earlier this year, furniture giant IKEA launched a collection of home goods made partially from recycled worker uniforms collected from stores and distribution centers across Europe. The Växelbruk collection, as it’s called, is a pilot project exploring how to give a second life to used clothing and manage recycling processes within IKEA’s value chain.
Between 2020 and 2022, IKEA rolled out a redesigned uniform and in the process collected several pallets of obsolete uniforms, which were then turned into the raw material to create new textile goods. The collection includes 16 products, including curtains, cushion covers, throws and bags. The products were made by mixing fibers from the collected uniforms with rPET recycled polyester to ensure desired color schemes and required quality standards.
“Through the Växelbruk pilot project, IKEA aimed to test and learn how to turn textile waste into secondary raw materials for new products,” said Lena Julle, sustainability manager. She added that the project “is an example of entrepreneurship that challenges current practices and develops ways of working for recycling.”
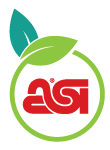
Promo for the Planet is your destination for the latest news, biggest trends and best ideas to help build a more sustainable and socially-responsible industry.